NOTTAM CAPABILITIES
The processes listed below serve as the foundation towards a highly integrated and scalable single-source operation. We are set to go live through the beginning of 2024.
Please subscribe below for launch updates and to provide input on the planned or future services you would be interested in utilizing. As a partnership-focused organization, your feedback is important to us.
NON-DESTRUCTIVE TESTING
Inspection methods that aid the human eye in identifying defects, discontinuities, and differences in part characteristics to ensure only acceptable components enter service or move down stream for subsequent processing.
Penetrant Inspection (PT) (FPI)
Magnetic Particle Inspection (MT) (MPI)
Component Upgrading - Defect Removal
Pre-penetrant Etching
Conductivity and Hardness Testing
METAL FINISHING
Liquid chemical processes that prevent the natural corrosion occurring in metals, while also improving part durability, abrasive resistance, cosmetic value, and adhesive properties.
Chromate Conversion (Chemfilm)
Type I - Hexavalent
Type II - Non-Hexavalent
Anodizing
Type I - Chromic
Type II - Sulfuric
Type III - Hardcoat*
*Color dyed & natural finishes applied to all types
Nitric Passivation
Electropolishing
Nital/Temper Etching
Descaling
Stress Relief & Hydrogen Embrittlement Baking
Chemical Stripping & Localized Repair
COATINGS
Application of high-performance primers, paints, powders and solid films of which protect parts from corrosion, environmental deterioration (UV/temperature), enhance part performance, and increase aesthetic value.
Liquid Paint (Primer/Topcoat)
Powder Coating
Dry/Solid Film Lubricant (DFL)
Part Marking: Silkscreen, Rubber Stamp, Ink Fill
Infrared (IR) and Oven Curing
Laser Engraving/Etching
Support Processes
Nottam Faber’s support processes serve as critical connection points between our core capabilities and further diversify the range of achievable, value-added outcomes.
Abrasive Blasting
Aluminum oxide, glass bead and plastic grit blast media
Precision Masking
Polyester tapes, silicon plugs and caps
CAD & CNC generated templates
Liquid spray and brush lacquers
Industrial Cleaning
Vapor Degreasing
Alkaline Cleaning
Solvent Cleaning
3-D Printing
Custom fabricated fixtures and packaging solutions
Future Process Considerations
Radiographic Inspection (RT) NDT
Ultrasonic Inspection (UT) NDT
Black Oxide MF
Zinc/Manganese Phosphate MF
Copper Plating MF
Cadmium Plating MF
Electroless/Electrolytic Nickel MF
Spin/Dip Application COATINGS
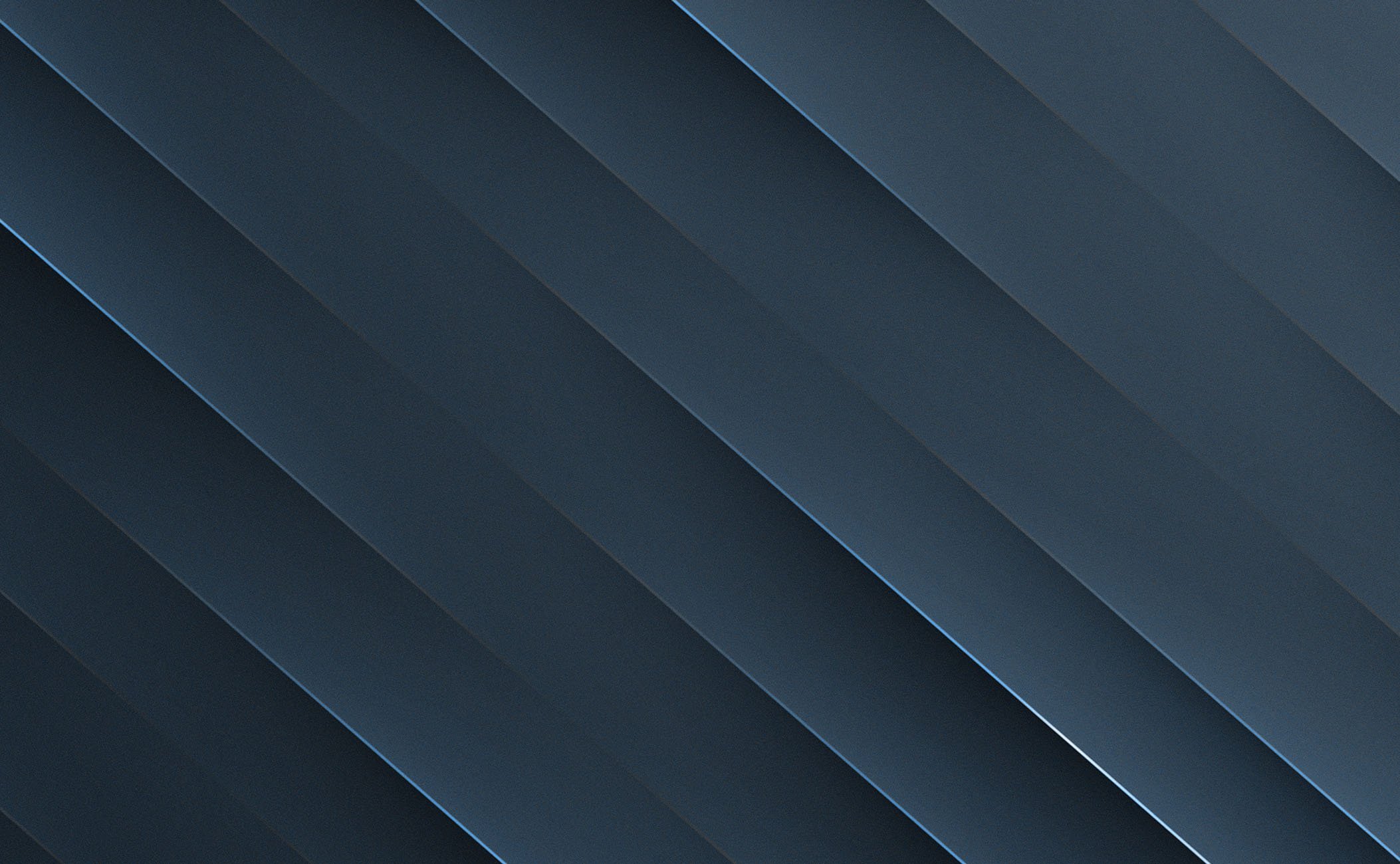